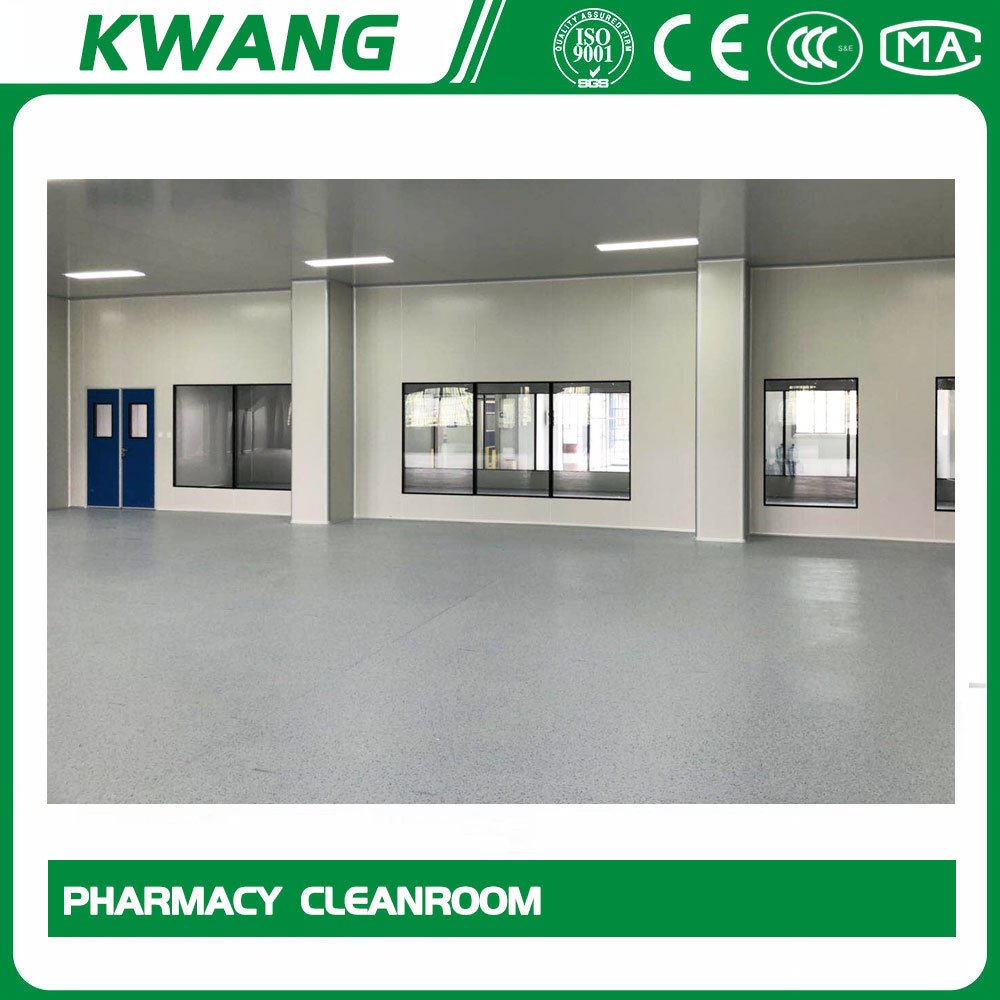
Biopharmaceutical Cleanroom
- Biopharmaceutical Cleanroom videoIn simple terms, a cleanroom is a controlled area within a wider facility that maintains a specific level of air particles and other contaminants. The three ways in which a cleanroom is clean are: The air quality is controlled. All surfaces and equipment are always cleaned to a certain standard.- Cleanroom Classifications:Biopharmaceutical CleanroomCleanrooms provide an enclosed environment with controlled levels of particulate matter (such as dust, vapours and airborne particles). Establishing a cleanroom involves a number of steps including engineering ...
- Biopharmaceutical Cleanroom video
In simple terms, a cleanroom is a controlled area within a wider facility that maintains a specific level of air particles and other contaminants. The three ways in which a cleanroom is clean are: The air quality is controlled. All surfaces and equipment are always cleaned to a certain standard.
- Cleanroom Classifications:Biopharmaceutical Cleanroom
Cleanrooms provide an enclosed environment with controlled levels of particulate matter (such as dust, vapours and airborne particles). Establishing a cleanroom involves a number of steps including engineering, manufacturing and control strategies. While they are used for a range of medical, scientific and manufacturing applications, we will provide a brief overview of cleanrooms used for pharmaceutical applications that do not handle potent chemicals or hazardous organisms.
Depending on the type of pharmaceutical product you manufacture and federal standards, you may or may not need a cleanroom. A clean area ventilated with filtered air can be used as an alternative to a clean room when producing non-sterile products. You should define your clean zone or cleanroom standards and procedures according to federal standards (e.g. US FED209E) or international standards (e.g. ISO 14644-1 and ISO 14698).
For sterile pharmaceutical products, cleanrooms are required to limit airborne particles and contamination from pharmaceutical products. The standards and requirements of a cleanroom are based on its classification and it is important that a room is properly classified as operators need to comply with all requirements and maintain the cleanliness standards for a given classification during operation.
- Biopharmaceutical Cleanroom Project Introduction
Medical device GMP sterile clean room
Clean area: 5000㎡ (sqm)
Cleanliness and differential pressure, reasonable layout of process flow, control of bacteria and dust Water supply and drainage, air and smoke exhaust, ground control, personnel and material control Process piping, laboratory construction, decoration materials and construction specifications control, other support and protection control.
- Biopharmaceutical Cleanroom Environment
Cleanroom Design Consideration
In addition to creating the ideal clean area or room, you must also take into account adjacent spaces such as corridors due to pressure cascades. An example is the production of pharmaceutical products such as capsules or tablets in a positive pressure environment. Due to the pressure difference between the two spaces, powders may escape from the clean area and enter the corridor. This is why it is important to design clean corridors that will inhibit the growth of microorganisms if they escape. When processing sterile or liquid pharmaceutical products, potential microorganisms must be kept out of the cleanroom, as they will find the environment and media conducive to microbial growth. In this case, the room will be under positive pressure and the adjacent space a dirty corridor.
In addition to the design of the rooms and corridors, the doors and their orientation must also be taken into account, as they need to maintain a pressure differential. As a general rule, all doors must open into the room with the higher pressure to prevent leakage. Please note that the springs in double swing doors can weaken over time, leading to air leakage beyond the design parameters. In addition, sliding doors or doors with recesses should be avoided as they can harbour and sometimes support the growth of micro-organisms.
Sources of Contamination
As previously mentioned, cleanrooms are designed to control the particulate content of the environment. Depending on the classification of the room, there is an acceptable level of particles per cubic foot or metre of air. For pharmaceutical applications, the main concern is microbial containment. As microbial contamination cannot be measured directly in real-time, it is assumed that "all airborne particles" includes all possible risks of microbial contamination.
Maintaining the Cleanroom Environment
While there are many national and international standards, classifications and requirements for cleanrooms, the three main aspects of a cleanroom are the control/quality of the air in the room, the internal surfaces and equipment in the room and the way the room is operated.
Firstly, a cleanroom requires a continuous supply of filtered air at a specific temperature and/or humidity level. Depending on your cleanroom classification, you may require more air as the classification requirements become more stringent." The ratio of 'fresh' air to recirculated air depends on the nature of the operation. If the operation produces high concentrations of vapours, gases or moisture, the room is to be supplied with 100% fresh air. To reduce the energy costs associated with air filtration and conditioning fresh air, you can recirculate the internal air by removing the particulate matter produced.
A well-designed system can provide both 'fresh' and recirculated clean air to a clean room. In a tightly controlled system, the amount of air supplied to the room flushes out an equal amount of air. To maintain a high pressure, the volume of air supplied to the room is greater than the volume of air discharged. Overall, a good system moves air throughout the room so that contaminants such as airborne particles and fumes are flushed out of the controlled environment.
Secondly, the internal surfaces of clean rooms and equipment should be smooth and impervious to water. They must be accessible and easy to clean, without any ledges or recesses that would create an environment prone to particulate build-up and microbial growth. In addition to being smooth and impermeable, they must also be constructed of a rigid material that will not crack or break. This prevents and limits the creation of additions.
Finally, the operation and maintenance of cleanrooms is the most effective way to control air quality. Personnel are considered to be the highest source of particulate matter and microbial containment. To maintain low particulate matter, only a limited number of trained personnel should be allowed in the room at specific times. In addition, appropriate cleanroom clothing and gowning procedures should be implemented. Production operations also generate particulate matter and preventing contaminants from being generated and escaping into the environment helps to maintain a controlled environment. Finally, regular cleaning and maintenance of facilities, equipment and ventilation systems will prevent the growth of particulate matter and microorganisms.
Clean rooms are classified according to the cleanliness level of the air inside the controlled environment. The clean room class is the level of cleanliness the room complies with, according to the quantity and size of particles per cubic meters of air. The primary authority in the US and Canada is the ISO classification system ISO 14644-1.
This ISO standard includes these clean room classes : ISO 1, ISO 2, ISO 3, ISO 4, ISO 5, ISO 6, ISO 7, ISO 8 and ISO 9. ISO 1 is the “cleanest” class and ISO 9 is the “dirtiest” class. Even if it’s classified as the “dirtiest” class, the ISO 9 clean room environment is cleaner than a regular room.
The most common ISO clean room classes are ISO 7 and ISO 8. The Federal Standard 209 ( FS 209E ) equivalent for these ISO classes are Class 10,000 and Class 100 000.
The old Federal Standard 209E ( FS 209E ) includes these clean room classes : Class 100,000; Class 10,000; Class 1,000; Class 100; Class 10; Class 1. This standard was replaced in 1999 by ISO-14644-1. It was withdrawn in 2001, but it is still widely used.
Clean rooms must also follow industry-specific and international standards. For example, EU GMP (A-B-C-D), applies to pharmaceutical products and USP (795, 797 and 800) to compounding pharmacies.
The GMP workshop is the special designed fully enclosed dust free room. It can not only remove the pollutants such as particle, harmful gas and bacterium but also control the temperature, cleanliness, pressure, air flow velocity and distribution, noise, vibration, illumination and static electricity to the needed level. No matter how the outer environment changes, the interior of the plant can still keep the characteristics meeting the original demands. Then, the product can be manufactured in a good environment.
- Other Types Of Cleanroom Classifications
Biopharmaceutical Cleanroom
Food Cleanroom