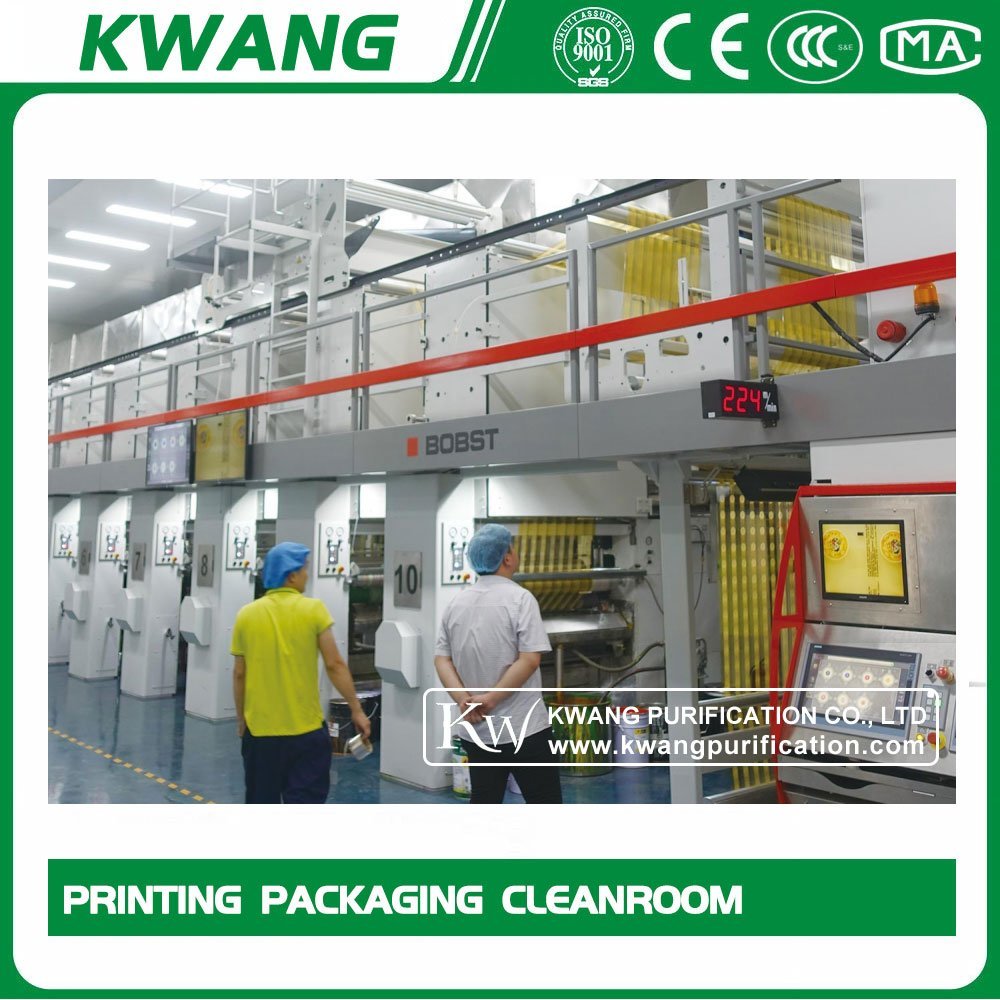
Printing Packaging Cleanroom
- Printing Packaging Cleanroom VideoA cleanroom is a controlled environment where pollutants like dust, airborne microbes, and aerosol particles are filtered out in order to provide the cleanest area possible. Most cleanrooms are used for manufacturing products such as electronics, pharmaceutical products, and medical equipment.Cleanroom Classifications:Printing Packaging CleanroomTake packaging printing factory as an example, if you can reach 100,000 class clean room standards, the quality of the product can be significantly improved. Life needs to use a variety of packaging bags, tradit ...
- Printing Packaging Cleanroom Video
A cleanroom is a controlled environment where pollutants like dust, airborne microbes, and aerosol particles are filtered out in order to provide the cleanest area possible. Most cleanrooms are used for manufacturing products such as electronics, pharmaceutical products, and medical equipment.
Cleanroom Classifications:Printing Packaging Cleanroom
Take packaging printing factory as an example, if you can reach 100,000 class clean room standards, the quality of the product can be significantly improved. Life needs to use a variety of packaging bags, traditional packaging materials are mostly offset printing method, there are certain defects, flexographic printing has developed rapidly in recent years, in foreign countries has been recognized as a 'most excellent and promising printing methods. Flexographic printing, is a prerequisite for the production of good quality packaging materials. In order to achieve flexographic printing, the workshop shall be made to meet the standard of 100,000-grade dust-free purification workshop to prevent and control dust, bacteria and other interference with printing, and to achieve constant temperature and pressure to create a good working environment and improve the quality of printed products, qualified rate.
Staff enter and leave through airlocks (sometimes including an air shower stage), and wear protective clothing such as hoods, face masks, gloves, boots, and coveralls. This is to minimize the carrying of particulate by the person moving into the cleanroom.
Printing Packaging Cleanroom Project Introduction
Class 100,000 printing and packaging dust-free cleanroom
Clean area: 9000㎡ (sqm)
From the beginning of the film blowing process, to the arrangement of printing equipment in place, the design of equipment supply and exhaust, to the dry lamination process, to the curing and slitting process, and finally to the bag-making workshop, no matter The human flow and logistics are precisely controlled to ensure that each link is dust-free and aseptic control of each step, which will make the finished product's asepsis better controlled. The asepsis of the finished products will be better controlled.
Printing Packaging Cleanroom Environment
Clean rooms are classified according to the cleanliness level of the air inside the controlled environment. The clean room class is the level of cleanliness the room complies with, according to the quantity and size of particles per cubic meters of air. The primary authority in the US and Canada is the ISO classification system ISO 14644-1.
This ISO standard includes these clean room classes : ISO 1, ISO 2, ISO 3, ISO 4, ISO 5, ISO 6, ISO 7, ISO 8 and ISO 9. ISO 1 is the “cleanest” class and ISO 9 is the “dirtiest” class. Even if it’s classified as the “dirtiest” class, the ISO 9 clean room environment is cleaner than a regular room.
The most common ISO clean room classes are ISO 7 and ISO 8. The Federal Standard 209 ( FS 209E ) equivalent for these ISO classes are Class 10,000 and Class 100 000.
The old Federal Standard 209E ( FS 209E ) includes these clean room classes : Class 100,000; Class 10,000; Class 1,000; Class 100; Class 10; Class 1. This standard was replaced in 1999 by ISO-14644-1. It was withdrawn in 2001, but it is still widely used.
Clean rooms must also follow industry-specific and international standards. For example, EU GMP (A-B-C-D), applies to pharmaceutical products and USP (795, 797 and 800) to compounding pharmacies.
The GMP workshop is the special designed fully enclosed dust free room. It can not only remove the pollutants such as particle, harmful gas and bacterium but also control the temperature, cleanliness, pressure, air flow velocity and distribution, noise, vibration, illumination and static electricity to the needed level. No matter how the outer environment changes, the interior of the plant can still keep the characteristics meeting the original demands. Then, the product can be manufactured in a good environment.
- Other Types Of Cleanroom Classifications